The Army needed a new vehicle to haul around its troops. Top brands were all cranking up models to meet the needs.
The winner was the High Mobility Multipurpose Wheeled Vehicle (HMMWV; colloquially known as Humvee). It largely replaced roles performed by original jeeps, their ambulance, and utility versions. Check out Military Humvee For Sale near you.
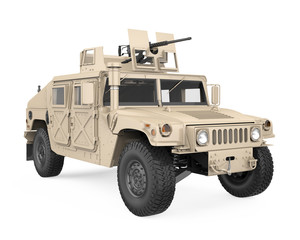
Origins
The military Humvee, also known as the HMMWV and the Hummer, grew out of necessity. The Army’s previous general-purpose vehicles were outmoded and not versatile enough to handle the changing nature of war. In the 1970s, the Army requested a new vehicle design that would meet demanding standards. The Army decided to choose HMMWV, which was nicknamed “Humvee” due to its hulking size and rugged appearance.
The Humvee was a huge success and soon replaced many of the other trucks in the military, from cargo vehicles to ambulances. The HMMWV could be modified to suit different tasks, with additions such as machine gun turrets and low-altitude air defense systems. Its rugged, all-terrain construction meant that it could easily negotiate rough terrain and was also suitable for use in urban conflict scenarios.
In the 1990s, they adapted the Humvee for civilian use, introducing the Hummer H1. This large, attention-grabbing vehicle was a hit with celebrities and became an icon of macho culture. It weighed about 8,000 pounds and got less than 10 miles per gallon, but its sturdy, attention-grabbing nature made it an instant hit with people who wanted to prove their manhood.
Humvees continued to serve in the military until they were eventually usurped by more advanced MRAP vehicles that could better withstand mines and ambushes. Today, however, Humvees are still used in a variety of roles and can be seen on the roads all over the world.
Almost every modern fighting force has some form of the Humvee in their arsenal, from local police departments to Navy SEALs. It is not unusual to see a Humvee in a parking lot, either, as the vehicle has become a symbol of the country’s military might. It has also been a fixture in many recent global conflicts, from Operation Desert Storm to the ongoing war in some countries. As such, it is a true military legend.
Functions
Throughout modern warfare, the Armed Forces have used a variety of motorized vehicles. Among them are the weird armored cars of World War I, the jeeps of WWII, and the more advanced Mine-Resistant Ambush Protected Vehicles (MRAP) of today. However, the Humvee is perhaps the most recognizable to the public. The vehicle has been on the front lines of nearly every conflict since 1989 and is still in use around the globe. It has conquered mud, sand, rocks, and snow and has been the backbone of the Army’s wheeled fleet. It has evaded detection by enemy forces and carried injured soldiers to safety. It has also helped take out enemy tanks. Perhaps no other military vehicle represents the Army as well as the Humvee.
Known officially as the High Mobility Multipurpose Wheeled Vehicle, or HMMWV, the Humvee was first created by the company in 1979. The company won a contract to design the vehicle after other companies submitted prototypes. Originally, the military wanted a light-duty utility vehicle that was capable of traversing rough terrain. Its body was designed to be easily modified for different missions, and it could carry a wide range of weapons.
The Humvee is a great example of how the military takes advantage of commercial technologies. The military was able to build an off-roading vehicle that was similar to popular consumer 4x4s at the time, and it added features like an onboard heater to keep the occupants warm during winter. It also included a rear air conditioning unit to cool the interior in hot weather.
Over the years, a variety of Humvee variants have been developed. They can be customized for a specific mission, from cargo and troop transport to ambulances. They can be equipped with everything from mounted machine guns to wire command-guided anti-tank missiles. They can even tow artillery, like the M119 howitzer.
In addition to its military uses, the Humvee is a popular civilian vehicle. Civilians can purchase the vehicles through government surplus auctions. They can also be purchased on consignment, which means that they may have already been properly inspected and registered by the previous owner. Although the military has replaced many Humvees, the Humvee will always be a military icon.
Variations
The original military vehicle that gave rise to the Humvee is the HMMWV or High Mobility Multipurpose Wheeled Vehicle. It was the replacement for the aging brand that had served in the military for decades. The Army sought a vehicle that would be able to carry a large variety of weapons and could perform several different types of missions. After testing and revisions, the Army chose the HMMWV from the company. This vehicle was given the Hummer name by soldiers, and it became a cultural icon.
While the HMMWV did well in desert conditions during Operation Just Cause and during the initial assault on forces in the Gulf War, it proved its mettle when it became the main ground transport vehicle. It’s this conflict that helped establish the Humvee as a global symbol of power and aggression.
With the onset of the War on Terror, however, the Humvee had to take a back seat to more sophisticated asymmetric warfare. Its aluminum body was paper thin against small arms fire and roadside improvised explosive devices. It was also a poor choice for cramped, urban streets that made it a prime target for ambushes.
Despite these challenges, the Humvee remains a key component of the modern military’s fleet. It’s used by troops around the world and is a familiar sight during operations in some countries. It has also inspired a plethora of civilian adaptations.
The company continues to make Hummer-based vehicles for a wide range of military applications. They also partner with international defense contractors to develop versions for other nations. One modification is used for surveillance, reconnaissance, escort, and troop carrier duties while the other is equipped with an armored turret to protect against light anti-tank weapons.
Interestingly, the HMMWV is still in service with the military, even though the Pentagon is phasing it out. The new Joint Light Tactical Vehicle (JLTV) has better armor, a more powerful engine, and better off-road handling. The JLTV is a more versatile vehicle that can handle the same types of missions as the Humvee, but it’s faster and gets much better fuel economy.
Final Words
After a few decades on the battlefield, it’s safe to say that the Humvee has earned its keep. This rugged, funny-looking military vehicle has conquered mud, sand, rocks, snow, and even the ocean floor. It’s pulled trailers down the highway and evaded detection in the desert. It’s been dangled from CH-53 helicopters, taken to the seas with Marine Expeditionary Units, and even jumped continents in transport aircraft. But now it’s time to pass the torch. The Humvee is being replaced by a new model called the Joint Light Tactical Vehicle, or JLTV. But while the JLTV is a better off-roader, the Humvee has a lot going for it as well.
It all started in 1979 with a request from the Pentagon for a true do-anything workhorse that could replace multiple vehicles and handle modern warfare. The military had been using other civilian off-the-shelf 4×4 trucks, but they weren’t up to the task. These trucks rumbled across rough terrain but didn’t have enough cargo space for all of the equipment that service members needed.
In response, the company began design work on the HMMWV in July 1980 and had the first engineering prototypes ready for testing two years later. Despite its silly name, the Pentagon was wowed by the H1 and snatched up 55,000 of them immediately.
But in the years that followed, it became clear that the Humvee wasn’t suited to combat against asymmetrical armies like the ones it would face. It was a great vehicle for whisking soldiers and Marines over wide expanses of sand but failed miserably in the cramped streets of cities. And while the aluminum body of the Humvee might have been able to shrug off small arms fire, it couldn’t take on roadside improvised explosive devices or rocket-propelled grenades.
To make its military vehicles more effective, the Pentagon decided to add armor to them. Adding armor to a Humvee increases its load capacity and makes it more resistant to damage, but it also adds weight and reduces fuel efficiency. This was a big deal in the era of high gasoline prices and growing environmental concerns. So, the Pentagon decided to create a new variant of the Humvee that had both armor and increased fuel economy.