Cabinet Refinishing Sacramento is great for those who want to update their kitchen without the cost of replacement. Our experienced technicians can give your cabinets a new coat of stain, restoring the original beauty and addressing minor surface damage like scratches and nicks.
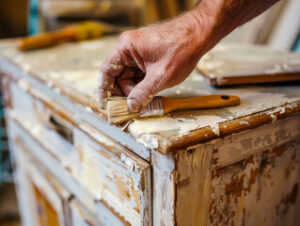
However, refinishing limits you to your existing cabinet structure—if you were looking for a different door style, refacing would be required.
Cabinet Refinishing is the perfect spring project to freshen up your home. Not only is it cost-effective compared to a total kitchen replacement, but it’s also environmentally friendly. Ripping out existing cabinets and putting up new ones has the added benefit of diverting waste from landfills. This is especially important since the materials used in cabinet construction aren’t renewable.
With the right preparation and care, a paint job should last a good amount of time before starting to fade or peel. However, even the best paint jobs can’t withstand contact with hands and other kitchen surfaces, as well as the repeated opening and closing of cabinet doors. That’s why NHance offers staining services that last longer than paint.
Staining can make a huge difference in the appearance of cabinets, enhancing natural wood grains and textures with colors that complement your home’s style and décor. In addition, sanding and other techniques can help remove scratches and scuffs, creating a smooth surface that’s resistant to stains. There are multiple ways to personalize your cabinet refinishing, including glass panels and crown molding that add visual interest and storage enhancements like pull-out drawers.
Refacing involves replacing the cabinet exteriors with a new veneer and installing a new set of doors and hardware. The result is a sleek, modern aesthetic that’s ideal for homeowners who want to update their kitchen with minimal effort. It can also be a more cost-effective alternative to a complete kitchen remodeling project, but can be constrained by the current cabinet layout and may overlook some functional or structural concerns.
The refacing process can be completed in a shorter timeframe than refinishing, making it a convenient option for homeowners that are short on time. Additionally, refacing can be completed without removing the existing cabinet boxes, reducing the cost of installation and minimizing disruption to your daily life. Additionally, refacing can utilize the same cabinet boxes as refinishing, providing a similar aesthetic. However, this approach is limited by the original cabinet layout and can overlook some functional or storage concerns. Additionally, refacing often requires more extensive structural work, such as adding support beams, than refinishing.
Time-Saving
Cabinet refinishing is much quicker than complete replacement, meaning that you can use your kitchen again in less time. This process is also a green option, since you’re not sending your old cabinets to the landfill and instead repurposing them for a new look that fits your current design vision.
When working with paints and stains, it’s essential to have proper ventilation in your workspace. This can be achieved by opening windows, using fans, or setting up exhaust systems. This will minimize fumes and promote airflow, preventing the build-up of dust that can stick to wet surfaces. It’s also important to cover any nearby surfaces that could get wet or be impacted by the paint or stain. Additionally, it’s important to allow enough time for the finishes to dry completely before reassembling the cabinets and reinstalling any hardware.
While it’s possible to refinish cabinets on your own, hiring professionals is often the best option for high-quality results that last. Refinishing professionals have the knowledge and experience to avoid costly mistakes that can arise from a DIY project, including improper surface preparation, improper application of finishes, and insufficient drying and curing times. Additionally, professionals work efficiently to minimize downtime and disruptions to your daily routine.
Choosing the right color can make your space feel warm and inviting, while highlighting any special architectural features or unique designs. You can choose a light shade that brightens the room or opt for a darker finish that adds warmth and depth. If you’re unsure of what color to choose, it’s helpful to consult with an interior designer who can help you select the perfect hue for your home.
The cabinet refinishing process begins with cleaning the cabinets to remove any grime or grease. Once the surfaces are clean, they can be primed to ensure that the new finish adheres properly. Once the primer is applied, a new coat of stain or paint is then applied. Multiple coats may be needed for a rich and even finish. After the final finish has been applied, a sealant is typically added to protect it from future damage and stains.
Versatile
Cabinet refinishing is a versatile option for homeowners who want to change the style of their kitchens without spending a fortune. By sanding, repainting, and varnishing your cabinets, you can breathe new life into them while redefining the style and character of your home.
You can choose from a variety of finishes for your cabinets, including matte, satin, semi-gloss, and high-gloss. It’s also possible to use a different color for each cabinet door and drawer front, so you can customize the look of your kitchen to suit your personal preferences. With so many options available, you’re sure to find the perfect look for your home.
The cabinet refinishing process takes several days to a few weeks to complete, depending on the size of your kitchen and the complexity of your chosen finish. During this time, you will need to clear out your kitchen and protect your countertops and appliances with covers. You may also need to set up a temporary kitchen space for the duration of the work. It’s also important to take your time while applying each coat, as rushing through the process can result in uneven paint or varnish coverage.
One of the primary benefits of Cabinet Refinishing is that it is much more budget-friendly than replacing your cabinets. This is because it utilizes your existing cabinet structures and focuses solely on the exterior surfaces, rather than replacing them altogether.
Cabinet refacing is another popular remodeling choice for homeowners in Ridgewood who want to completely change the appearance of their cabinets. Unlike refinishing, refacing replaces the existing cabinet doors and drawer fronts, as well as adds new material or veneer to the cabinet boxes themselves. This allows for a full transformation of the cabinet style and design, but it’s more expensive than refinishing.
Cabinet refinishing is an excellent option for older homes that have original cabinets with higher-quality materials and craftsmanship than modern-day alternatives. This type of renovation can bring back that timeless appeal without sacrificing functionality or quality, which is especially important for Ridgewood homeowners who are looking to sell their homes in the future. In addition, refinishing can be done more quickly than replacement, which can require demolition and render your kitchen unusable for weeks.
Customizable
Cabinet refinishing is the perfect solution for those who want to give their cabinets a facelift without replacing them. This process involves stripping and sanding your existing cabinets before applying new stain or paint. This provides a smooth, durable finish that will last for years to come. It also allows you to customize the color of your cabinets, as well as add special finishes such as glazes and distressing. This gives you an endless amount of customization options, allowing you to create a look that perfectly suits your home’s style and decor.
While refinishing may seem simple enough to do yourself, it is recommended that you hire a professional for the best results. A professional will ensure that your cabinets are properly prepared, including cleaning, sanding, and priming. This is important because if the surfaces are not properly prepared, they will not be able to hold a new coat of paint or stain. In addition, a professional will use high-quality materials, which is essential for a long-lasting finish.
When refinishing your cabinets, it is important to take the time to mask off any areas you don’t want to paint, such as hinges, handles, and knobs. This will protect them from the paint and prevent accidental damage. You should also let the first coat dry for 3-4 hours before applying a second coat. Finally, it is a good idea to apply a protective sealant to your cabinets after the second coat has dried, which will help them resist wear and tear over time.
There are two primary ways to update your kitchen’s cabinets: refacing or refinishing. Each method offers its own unique benefits, but it’s crucial to understand the difference before you choose which option is right for your home. Refinishing is an excellent choice for those who are looking to give their cabinets a facelift without breaking the bank. It is also a more eco-friendly option than completely replacing your cabinets. Refacing, on the other hand, is a more comprehensive update that includes replacing the doors and drawer fronts with a new veneer. This can offer a more dramatic upgrade in terms of both style and functionality, but it will be more costly than refinishing.